business resources
Essential Factors to Consider When Purchasing Industrial Pumps
18 Jan 2025, 9:27 am GMT
When it comes to choosing an industrial pump, a myriad of factors must be taken into account to ensure optimal performance and efficiency. Industrial pumps play a crucial role in the transportation of liquids in numerous sectors, including manufacturing, construction, and wastewater management. Selecting the right pump can significantly impact not just the production process but also operational costs and maintenance. Understanding the pivotal aspects to consider will streamline the purchasing process and lead to better long-term results.
Types of Industrial Pumps
The first step in the purchasing process involves recognizing the various types of industrial pumps available on the market. As explained by experts from DAE Pumps, pumps are generally categorized into two main types: positive displacement pumps and centrifugal pumps. Positive displacement pumps are known for their ability to move a fixed amount of fluid with each cycle. These pumps are particularly useful when handling viscous liquids or fluids that require consistent flow rates. Conversely, centrifugal pumps rely on rotational energy to move liquids, making them suitable for low-viscosity applications. Understanding the specific requirements of your application will guide you in selecting the appropriate type of pump. Furthermore, various subtypes exist within these categories, such as gear pumps, diaphragm pumps, and screw pumps, among others. Analyzing the specific needs of your operation, including the viscosity of the fluids, the pressure requirements, and the flow rates, is vital when determining the most suitable pump type.
Application Requirements
An essential aspect of pump selection lies in evaluating the specific application requirements. Each industry has unique demands that can significantly influence pump choice. Factors such as temperature, pressure, and the nature of the fluid being pumped must be taken into consideration. For example, in the oil and gas sector, the ability to handle abrasive or corrosive materials is critical. Choosing a pump made from high-quality materials, capable of withstanding harsh environments, ensures reliability and durability. Analyzing the intended application’s nuances will help pinpoint the most effective pump for achieving desired outcomes. Custom specifications may arise, particularly in specialized industries such as food processing, pharmaceuticals, or chemical manufacturing. In these cases, collaborating with experienced manufacturers who understand industry standards is crucial. Understanding what materials comply with hygiene and safety regulations can mean the difference between a successful operation and significant losses due to non-compliance.
Efficiency and Energy Consumption
Efficiency plays a pivotal role in industrial pump selection, as it directly affects operational costs. An efficient pump not only minimizes energy consumption but also reduces the wear and tear on associated machinery. Substantial savings can be achieved by investing in a pump designed for optimal energy efficiency, with many modern models utilizing advanced technologies to enhance performance. According to the U.S. Department of Energy, over 20 percent of all electricity consumed in the United States is used to power pumps. Investing in energy-efficient technologies can yield considerable cost savings, making it a smart business decision. This aspect is particularly pressing as industries are increasingly held accountable for reducing energy consumption and minimizing their environmental footprints. Investigate the efficiency ratings of potential pump options. Many manufacturers provide metrics on centrifugal and positive displacement efficiencies, allowing for informed decisions. Seeking out options that boast lower operating costs can enhance competitiveness in the marketplace while contributing positively to environmental sustainability.
Maintenance and Reliability
While selecting the right pump is crucial, ensuring long-term reliability involves understanding the maintenance requirements of various pump types. Regular maintenance not only enhances the longevity of the pump but also guarantees consistent performance. Understanding how accessible replacement parts are is key. Pumps that require specialized components may lead to longer downtimes if those parts must be custom-made or imported. Opt for pumps with a reputation for reliability and a broad availability of parts in the local market to ensure minimal disruption to your operations. Furthermore, consider the complexity of maintenance tasks associated with each pump type. Some pumps may require regular lubrication or seal replacement, while others may have self-lubricating capabilities. Familiarize yourself with the maintenance expectations of potential pumps before making your purchasing decision. By doing so, you can preemptively address any challenges that may arise post-installation.
Cost Considerations
Evaluating the total cost of ownership is a vital step in the purchasing process. This involves taking into account not only the initial purchase price but also operational costs, maintenance expenses, and potential downtime due to equipment failure. When comparing pumps, ensure you conduct a total cost analysis, which involves looking at operational costs over the expected lifecycle of the pump. While a lower initial price may be appealing, it could lead to increased expenses over time due to higher energy consumption or maintenance needs. Seek to work with suppliers and manufacturers who can provide transparent information on the lifetime costs of their products. This collaborative approach aids in making informed decisions that align with budgetary constraints while still meeting performance and quality requirements.
Supplier Reputation and Customer Support
The credibility of the supplier or manufacturer is another critical factor when selecting industrial pumps. Researching and evaluating a supplier’s reputation can lead to significant advantages. Look for those with strong customer service, extensive industry experience, and positive reviews from previous clients. Engaging with suppliers who offer comprehensive support services can make a difference, especially when troubleshooting or requiring urgent maintenance assistance. Strong partnerships with reliable suppliers can enhance operational efficiency by ensuring timely service and solutions. Furthermore, check if the suppliers offer training for staff on pump operation and maintenance. This can help to minimize human error during operations, allowing your equipment to perform optimally and thereby extending its lifespan.
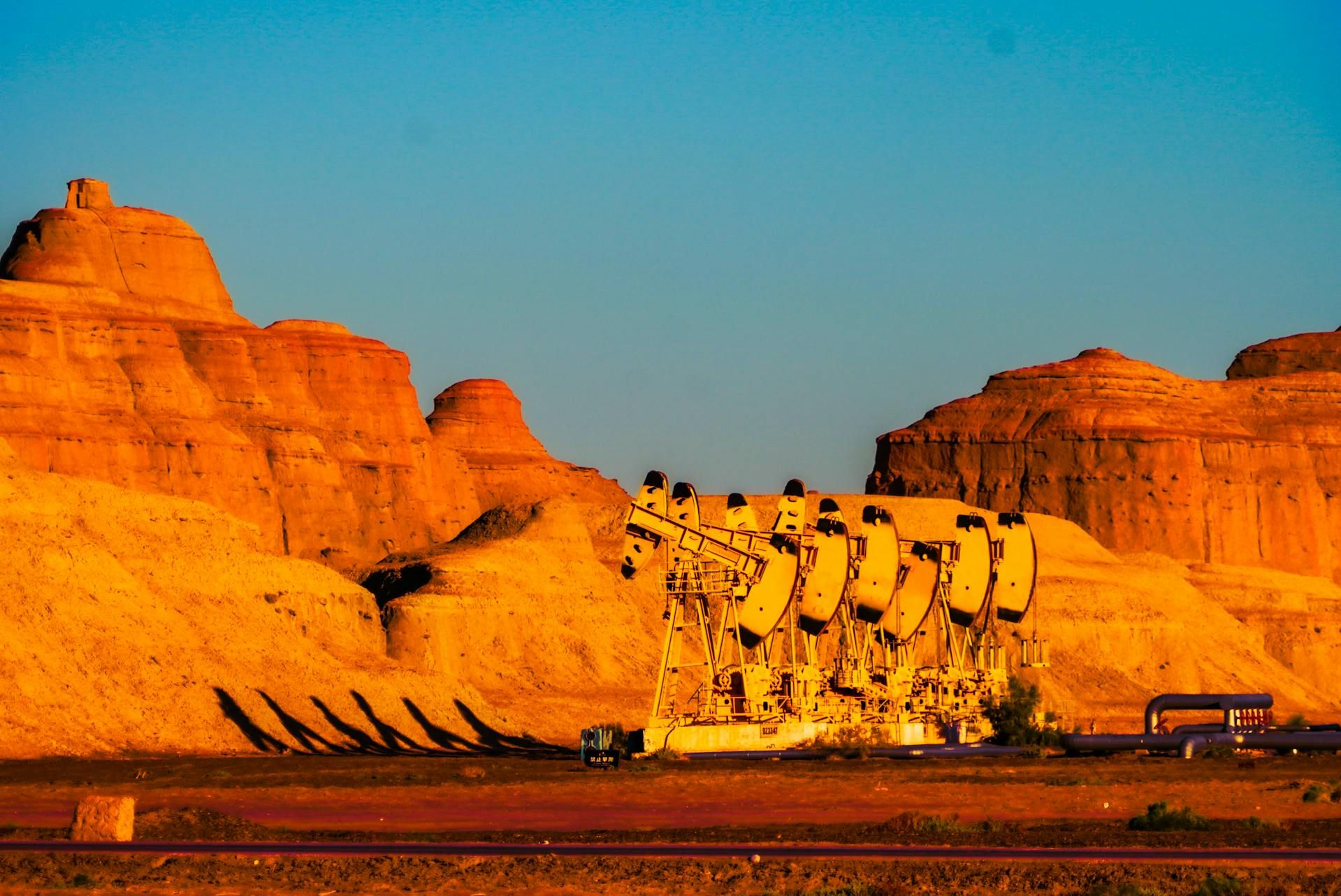
Technology and Innovation
In the rapidly evolving industrial landscape, staying abreast of technological advancements is crucial. Many modern pumps now incorporate innovative technologies that enhance their functionality and performance. For instance, smart pumps equipped with sensors can provide real-time data on performance metrics, allowing operators to make proactive decisions regarding maintenance and optimization. With innovations like predictive analytics and IoT integration, industries can derive significant insights from their pump operations. Such advancements help to bolster efficiency, reduce downtime, and optimize resource allocation. Evaluating the available technological options can assist in identifying pumps that will deliver sustainable performance. Given the prevalence of proprietary technologies, ensure compatibility with existing systems within your facility. This consideration is essential to seamlessly integrate new pumps into your processes without incurring additional costs for enhancing infrastructure.
Choosing the right industrial pump requires careful consideration of numerous factors, including the type of pump, application requirements, efficiency, maintenance needs, and supplier reputation. By understanding these essential aspects, businesses can make informed decisions that enhance productivity and sustainability in their operations. A systematic approach to pump selection not only boosts operational performance but also leads to cost savings and long-term reliability.
Share this
Arthur Brown
Writer
A dad of 3 kids and a keen writer covering a range of topics such as Internet marketing, SEO and more! When not writing, he's found behind a drum kit.
previous
Top Funding and Accelerator Programs for Startups in 2025
next
The Importance of Non-Destructive Testing in Ensuring Quality and Safety