business resources
How Digital Twins Redefine Factory Optimisation
25 Jan 2024, 7:52 pm GMT
Manufacturers worldwide are grappling with the challenges of meeting demand amidst talent shortages, supply chain disruptions, and the need for cost-effective decision-making. Digital twins, particularly in the form of real-time virtual representations of factories, have become indispensable tools for overcoming these hurdles. These digital replicas allow manufacturers to simulate real-time conditions, conduct "what-if" analyses, and optimise various aspects of their operations.
The 2022 survey of senior executives, carried out by McKinsey, within the industrial sector, had revealed that manufacturing leaders are grappling with two critical challenges: material and labor constraints stemming from escalating costs and talent shortages, and the pressing need for enhanced production visibility. This includes improvements in demand forecasting, inventory processes, manufacturing flexibility, and real-time monitoring of the factory floor.
The survey underscores the growing recognition of factory digital twins as a highly sought-after technological solution to address these formidable issues. Among respondents from various industries, a significant 86 percent expressed the view that a digital twin holds relevance for their organisation. Furthermore, 44 percent of respondents reported having already implemented a digital twin within their operations, while an additional 15 percent conveyed plans to deploy this technology in the near future.
Predictive maintenance using digital twin technology
Creating a digital twin of physical machinery and systems can enable enterprises to monitor real-time data and performance parameters. This allows for the early detection of potential equipment failures and anomalies.
Predictive maintenance goes beyond traditional, schedule-based approaches, as it leverages data analytics and machine learning algorithms to forecast when maintenance is needed. The digital twin serves as a dynamic model that simulates the actual operating conditions, enabling organisations to predict and prevent issues before they impact production.
Siemens, a global leader in energy technology, has created a virtual replica of the entire production process to simulate and analyse different scenarios and optimise efficiency. The digital twin predicts equipment failures before they occur, allowing for proactive interventions. This not only minimises the downtime but also extends the lifespan of critical components, resulting in significant cost savings.
How digital twin technology enhances quality and production?
By creating a virtual replica of physical assets, processes, or systems, enterprises gain unparalleled insights into real-time operations. This enables continuous monitoring and analysis, facilitating the early detection of potential issues and deviations from optimal performance.
GE Aviation has harnessed the power of digital twins to closely monitor real-time performance. This includes identifying potential quality issues during production and optimising manufacturing parameters for enhanced component quality. The digital twin approach ensures that each component meets stringent quality standards, contributing to the overall reliability and safety of aircraft engines.
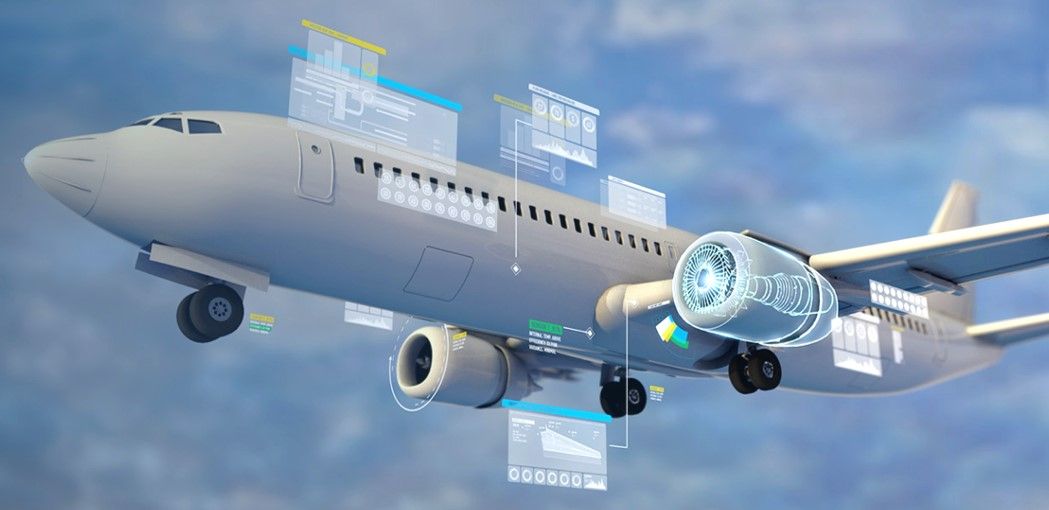
Real-time monitoring for operational excellence using digital twin technology
The digital twin technology enables organisations to simulate different scenarios, identify bottlenecks, and streamline workflows, ultimately enhancing overall production efficiency. It also contributes to improved quality by ensuring that products meet stringent standards. They enable real-time monitoring of product characteristics and allow for adjustments during the design and production phases.
Bosch Rexroth, for instance, a leader in drive and control technologies, has implemented digital twins in its "Factory of the Future" initiative. The digital twin allows for real-time monitoring of manufacturing processes, providing valuable insights for operational excellence. From predictive maintenance to energy efficiency improvements, Bosch Rexroth's digital twin ensures that the factory operates at peak performance. This real-time visibility enables quick adjustments, contributing to overall efficiency gains and cost savings.
Agile manufacturing for market responsiveness
By seamlessly integrating real-time data, simulation capabilities, and advanced analytics, agile manufacturing enables companies to swiftly adapt to dynamic market conditions, providing a holistic view on the entire lifecycle of the product. This technological synergy fosters a responsive and adaptive manufacturing environment, allowing companies to anticipate market fluctuations, streamline production processes, and promptly implement changes.
Consumer goods giant Procter & Gamble has integrated digital twin technology into its manufacturing operations, enhancing agility and responsiveness. Through virtual models of production lines, P&G can simulate different scenarios, identify bottlenecks, and optimise production schedules. This agile approach enables P&G to adapt swiftly to changing market demands, improve resource utilisation, and maintain a competitive edge in the dynamic consumer goods industry.
Streamlining production planning and maintenance
Digital twins enable simulation of various scenarios, facilitating robust decision-making to enhance resource utilisation, minimise bottlenecks, and optimise overall production workflows. According to McKinsey study, integrating the technology into the existing manufacturing execution system (MES) platforms, Internet of Things (IoT) devices, and inventory databases help enterprises in determining the optimal sequencing of different product lines, while minimising the downtime.
BMW, a renowned automaker, utilises digital twin technology to streamline various aspects of its manufacturing operations. By creating virtual replicas of production processes, BMW can simulate and analyse the entire manufacturing workflow. This includes optimising production planning, predicting maintenance needs, and ensuring seamless coordination across production lines. The digital twin approach contributes to enhanced efficiency, reduced downtime, and continuous improvement in automotive manufacturing.
Enhancing manufacturing efficiency
In the contemporary industrial landscape, manufacturers are leveraging cutting-edge solutions such as automation, artificial intelligence, and digital twin technology to revolutionise their operations. Through the implementation of smart manufacturing practices, organisations can achieve seamless coordination between machines, streamline production workflows, and reduce manual intervention.
Utilising digital twin technology, a metal fabrication plant successfully identified optimal batch sizes and production sequences to enhance the efficiency of scheduling across its four parallel production lines. In managing the intricate nature of its operations, the plant employed an AI-driven agent trained in reinforcement learning (RL) to construct the most advantageous order sequence based on insights derived from the digital twin. This application of RL algorithms resulted in notable cost reductions and improved yield stability compared to traditional manual scheduling methods.
Moreover, the integration of digital twin technology with RL algorithms has set a new benchmark for the industry, showcasing the potential for even greater automation and efficiency gains. Consumers and investors can explore KNS Metals Perth and other reputable companies that exemplify the forward-thinking approach in steel fabrication, leveraging advanced technologies to stay competitive in a rapidly evolving market.
ArcelorMittal, a global steel and mining giant, leverages digital twins to optimise its steel manufacturing processes. Virtual replicas of production lines allow ArcelorMittal to analyse real-time data, predict equipment failures, and optimise operational parameters.
Developing a modular scalable digital twin
The development of a modular and scalable digital twin is a strategic imperative for enhancing operational efficiency. Digital twins integrate diverse data sources, employing a modular and scalable tech stack that forms the foundation of this transformative technology. Manufacturers are faced with the choice between natively built digital twins and incorporating "starter packs," which serve as pre-designed components supporting interconnected data, providing user-friendly interfaces, or acting as optimisers for various production inputs.
A universally designed modular tech stack employs building block components with standardised interfaces, ensuring scalability and easy addition of new modules. A key element is the establishment of a single source of truth through a Unified Name Space (UNS) architecture, facilitating proper classification, structuring, and access to data, leading to consistent operational insights.
The tech stack's core involves sourcing, storing, and processing data, where production data from Programmable Logic Controllers (PLCs) and Manufacturing Execution Systems (MES) platforms forms the base. Inventory and demand data, whether from customers or Enterprise Resource Planning (ERP), are integrated, emphasising the critical need for systematic data cleaning to ensure reliable and repeatable modeling. Data service integration software then unites disparate streams into a common data pathway, creating a standardized language for integration. This approach, exemplified by the UNS architecture, simplifies the complexity of scaling up use cases.
Simulation software, such as discrete event simulation or natively built code, serves to create a virtual rendering of the factory floor for identifying bottlenecks and constraints through thousands of simulated production sequences. Finally, optimisation, facilitated by advanced techniques like genetic algorithms and machine learning, enables the digital twin to run millions of hypothetical production sequences, identifying optimal sequences that maximise productive time.
Recent advancements in optimisation techniques and machine learning are pivotal in revolutionising factory performance, as demonstrated by real-world examples showcasing a four percent reduction in total processing time through optimised sequencing at critical bottleneck stations.
Share this
Pallavi Singal
Editor
Pallavi Singal is the Vice President of Content at ztudium, where she leads innovative content strategies and oversees the development of high-impact editorial initiatives. With a strong background in digital media and a passion for storytelling, Pallavi plays a pivotal role in scaling the content operations for ztudium's platforms, including Businessabc, Citiesabc, and IntelligentHQ, Wisdomia.ai, MStores, and many others. Her expertise spans content creation, SEO, and digital marketing, driving engagement and growth across multiple channels. Pallavi's work is characterised by a keen insight into emerging trends in business, technologies like AI, blockchain, metaverse and others, and society, making her a trusted voice in the industry.
previous
The Role of Valve Actuators in Energy Efficiency
next
Signs Your Team Could Benefit from Executive Presence