business resources
How to Implement Lean Storage Practices in Your Warehouse
8 Sept 2022, 3:24 am GMT+1
In the fast-changing warehouse management sector, striving for efficiency and reducing waste is imperative. A compelling statistic underscores this need—the global warehouse automation market is expected to expand significantly, with forecasts predicting it to reach $41 billion by 2027. This growth highlights the essential requirement for warehouses to adopt lean practices that improve operational flow and cut down on waste.
Embracing lean principles helps warehouses address challenges and leverage them for expanded growth and improvement. By implementing these principles, you can turn your warehouse into an operation that is both more adaptable and quick to respond.
In this blog post, we’ll explore the essential strategies and steps that enable you to integrate lean storage practices into your warehouse, maintaining your competitiveness in a demanding market.
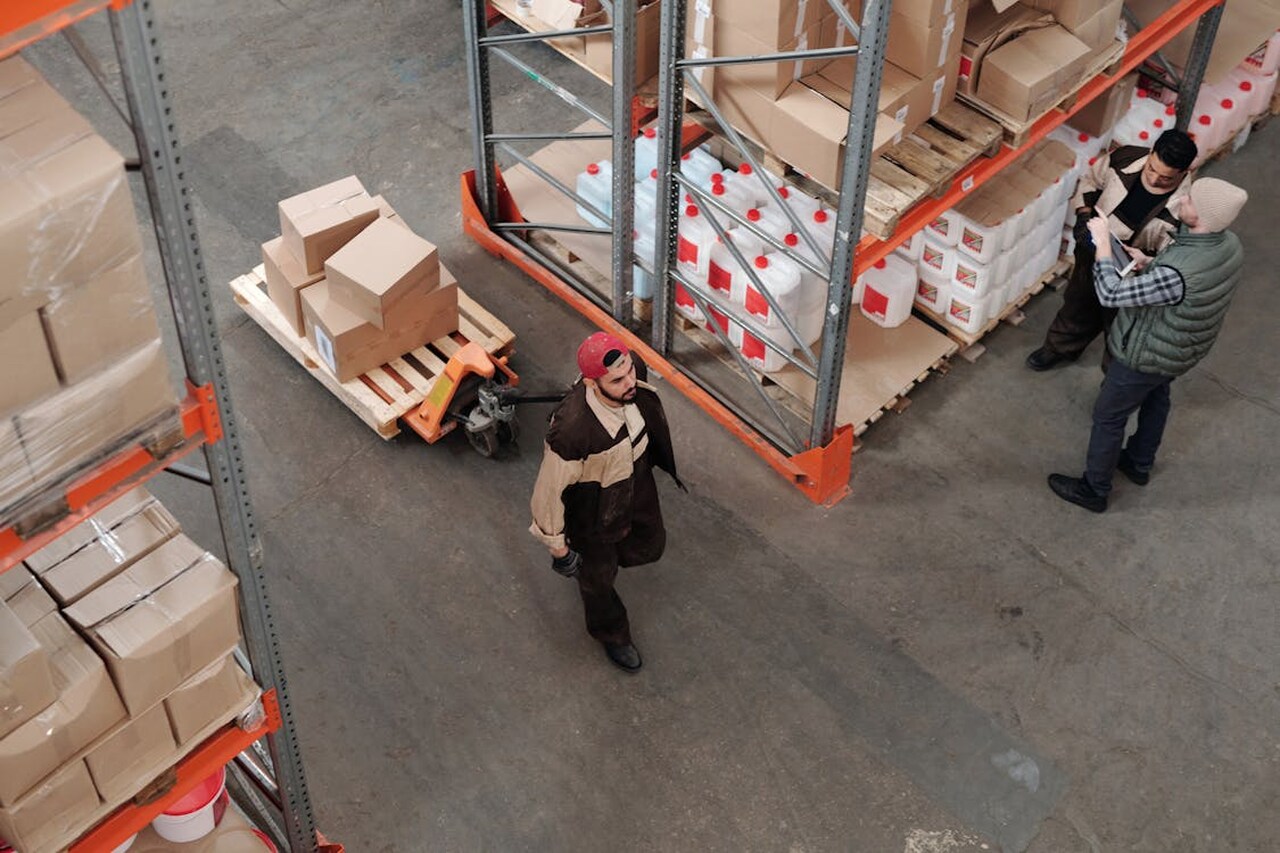
Assessing Current Storage Practices
The initial step in adopting lean storage involves a thorough assessment of your existing storage practices. This process includes examining how your facility receives, stores, and retrieves goods. Critical factors to review are the accuracy of your inventory, the condition of stored goods, and the efficiency of your storage layout. This evaluation will help pinpoint any inefficiencies or superfluous steps in your processes that could be streamlined or removed.
Optimizing Layout and Flow
Minimizing waste and enhancing efficiency is crucial, and optimizing your warehouse layout and flow plays a key role in this. A strategic layout ensures quick access to frequently needed items, minimizing unnecessary movement. Analyze the flow of goods from the receiving area through to storage, and finally shipping.
Incorporating durable solutions such as metal storage containers from trusted suppliers can boost this efficiency. These containers, known for their sturdy design and stackability, are excellent for organizing and safeguarding goods in areas with heavy traffic. The aim is to establish a smooth and logical flow that diminishes bottlenecks and reduces waiting times, thereby accelerating the entire process. Utilizing these metal storage containers also helps maintain inventory precision by keeping goods secure and orderly.
Implementing Inventory Management Techniques
At the heart of lean storage strategies lies effective inventory management. For instance, just-in-time inventory is a technique that streamlines operations by closely aligning inventory with demand. Adopting JIT inventory allows warehouses to avoid the drawbacks of overstocking, which uses up physical space and capital that could be better utilized elsewhere.
This approach demands precise coordination and communication with suppliers to ensure timely delivery of materials. Such precision reduces handling costs, storage needs, and risks associated with goods becoming obsolete or damaged in storage.
Successfully implementing JIT inventory involves transitioning from traditional inventory practices to a dynamic, demand-driven approach, significantly reducing waste and boosting operational responsiveness.
Continuous Improvement and Training
Lean principles represent an ongoing journey of enhancement, not a finite project. Sustaining and building upon the initial successes of lean practices requires continuous training and development of employees. Regular training sessions ensure that all staff members are current with the latest lean techniques and technologies.
Furthermore, fostering a culture of continuous improvement motivates employees to identify inefficiencies and propose viable solutions. This collaborative environment unveils hidden opportunities for efficiency gains and fosters a sense of responsibility and accountability among staff.
Workshops and regular feedback sessions are crucial in embedding this culture, ensuring that lean practices influence every aspect of warehouse operations. As new challenges emerge and the market evolves, revisiting existing processes is vital for maintaining efficiency and relevance.
Leveraging Technology for Lean Management
Today, technology acts as a vital support for lean practices in warehouse management. Advanced warehouse management systems (WMS) and various automation tools are crucial for enhancing inventory control and increasing workflow efficiency.
These systems provide detailed, real-time data that enables managers to make precise decisions about inventory levels, staff deployment, and effective space utilization. Automation technologies such as RFID and barcode scanning streamline data collection, significantly lowering the incidence of manual errors and accelerating operational activities.
Additionally, tools like automated storage and retrieval systems, as well as robotics, manage repetitive, strenuous tasks, improving safety protocols and reducing human errors, thus allowing employees to dedicate their efforts to more intricate and revenue-enhancing activities. By adopting these technological innovations, precision and efficiency are significantly improved, transforming lean management from a mere methodology into a sustainable operational norm.
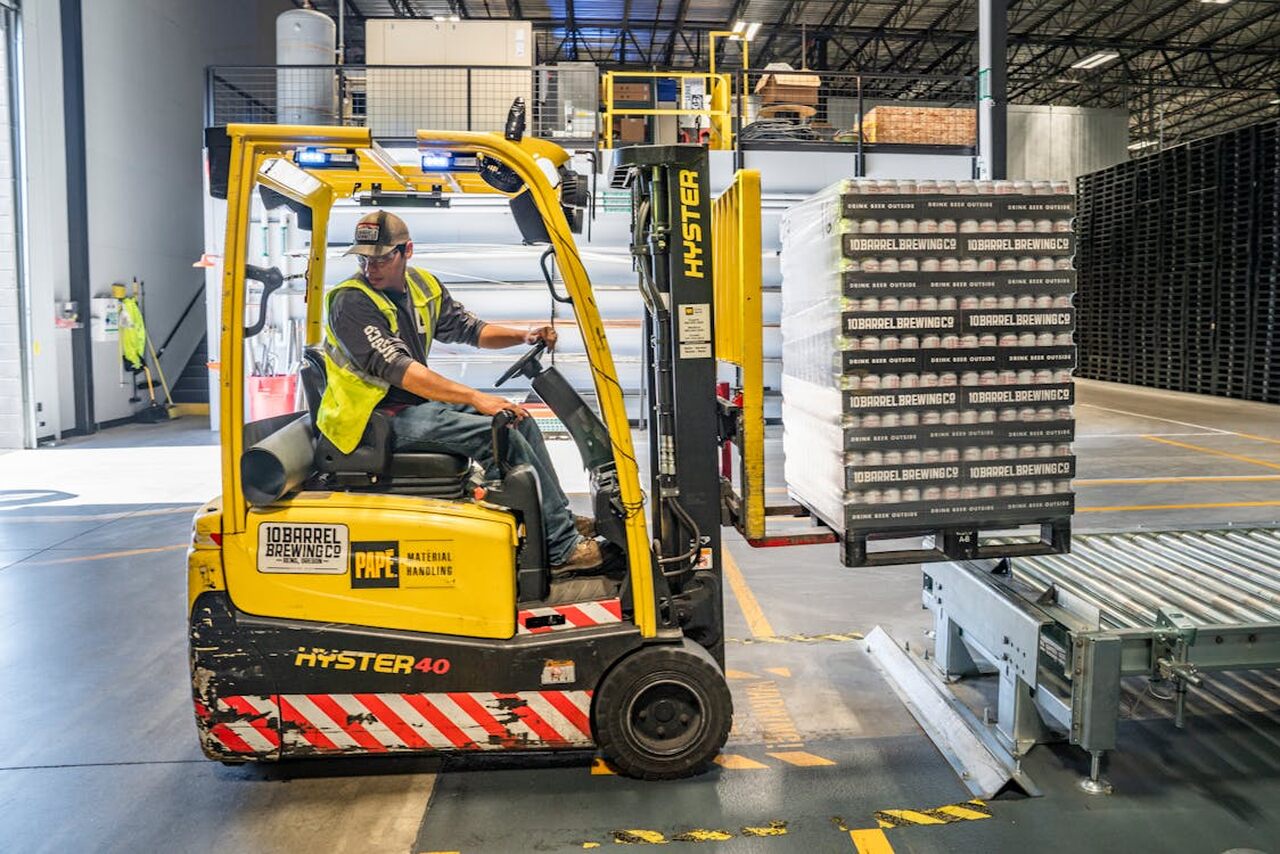
Conclusion
Adopting lean storage practices can greatly boost efficiency and cut down on waste within your warehouse operations. By evaluating your existing processes, refining your layout, executing effective inventory management, dedicating to ongoing enhancement, and utilizing technology, you can shape a more efficient and economically viable operation. Armed with the strategies and insights shared here, you can enact knowledgeable modifications that push your warehouse toward improved operational efficiency. It’s time to make your warehouse not only function better but also thrive in today's competitive environment.
Share this
Contributor
Staff
The team of expert contributors at Businessabc brings together a diverse range of insights and knowledge from various industries, including 4IR technologies like Artificial Intelligence, Digital Twin, Spatial Computing, Smart Cities, and from various aspects of businesses like policy, governance, cybersecurity, and innovation. Committed to delivering high-quality content, our contributors provide in-depth analysis, thought leadership, and the latest trends to keep our readers informed and ahead of the curve. Whether it's business strategy, technology, or market trends, the Businessabc Contributor team is dedicated to offering valuable perspectives that empower professionals and entrepreneurs alike.
previous
Impact of Chip Shortages on Consumer Electronics Prices
next
Virgin Awesometer drives rapid reaction