business resources
Shuttle Systems in Modern Warehouses
14 Feb 2025, 1:55 pm GMT
The concept of automated warehouse technology began in the 1960s with the first automated storage and retrieval systems (AS/RS). These systems used computer-controlled mechanisms to move products around the warehouse.
Since then, warehouse solutions have advanced dramatically, evolving from simple, basic racks to cutting-edge automation systems, including shuttle systems.
What Are Shuttle Systems?
Shuttle systems are warehouse conveying equipment that use mobile carts (shuttles) to move items like totes, trays, and cases from storage to their destination. The system usually has multiple shuttles in the storage level to access the products on that level. These shuttles are connected to lifts that help them travel the racking paths to pick up or drop off pallets at either end of the rack.
Shuttle systems work great in warehouses with low SKU counts and high throughput, where frequent pallet loading and unloading are common. They're also perfect for small warehouses that need order fulfillment and replenishment but don't have room for forklifts.
These systems make it easier to manage deep storage racks, speeding up the movement of goods in and out of the warehouse. By using every inch of storage space, shuttle systems help increase racking depth and height and reduce the number of aisles.
Due to their speed and accuracy, shuttle systems are widely used in industries like retail, e-commerce, and food and beverage. They facilitate faster order fulfillment and reduce waste with Fast-In, Fast-Out (FIFO) capabilities.
Technologies and Components That Make up a Warehouse Shuttle System
Here’s a quick breakdown of the key components that make a warehouse shuttle system tick:
- Shuttle vehicles: These are small, automated units that move goods both horizontally (on conveyor belts) and vertically (via lift systems) within storage racks. They use motors and sensors to follow predefined paths to get goods where they need to go—whether it's picking up or dropping off items at different racks.
- Racking Structure: These are specialized shelves designed to store goods efficiently. They are built vertically and provide the perfect track for shuttle vehicles to navigate when handling goods, maximizing storage space by going up instead of out.
- Control Systems: These are the brains of the operation. They include control panels and user interfaces that allow operators to monitor and manage the shuttle vehicles. They also help track goods and handle inventory, all from a centralized system that can be operated on-site or remotely.
- Pallets and Rails: These structures hold and guide transported goods and shuttle vehicles in a shuttle system. Rails keep shuttle vehicles on track and guide them along their path within the storage racks. Pallets serve as a solid base for transporting goods. Together, they ensure smooth navigation and handling of goods to improve efficiency.
- Sensors and Cameras: These smart devices track shuttle vehicles in real time and help them navigate the warehouse while avoiding obstacles. They ensure everything stays in motion and provide vital data to track exactly where each item is.
How Shuttle Systems Work (Product Retrieval)
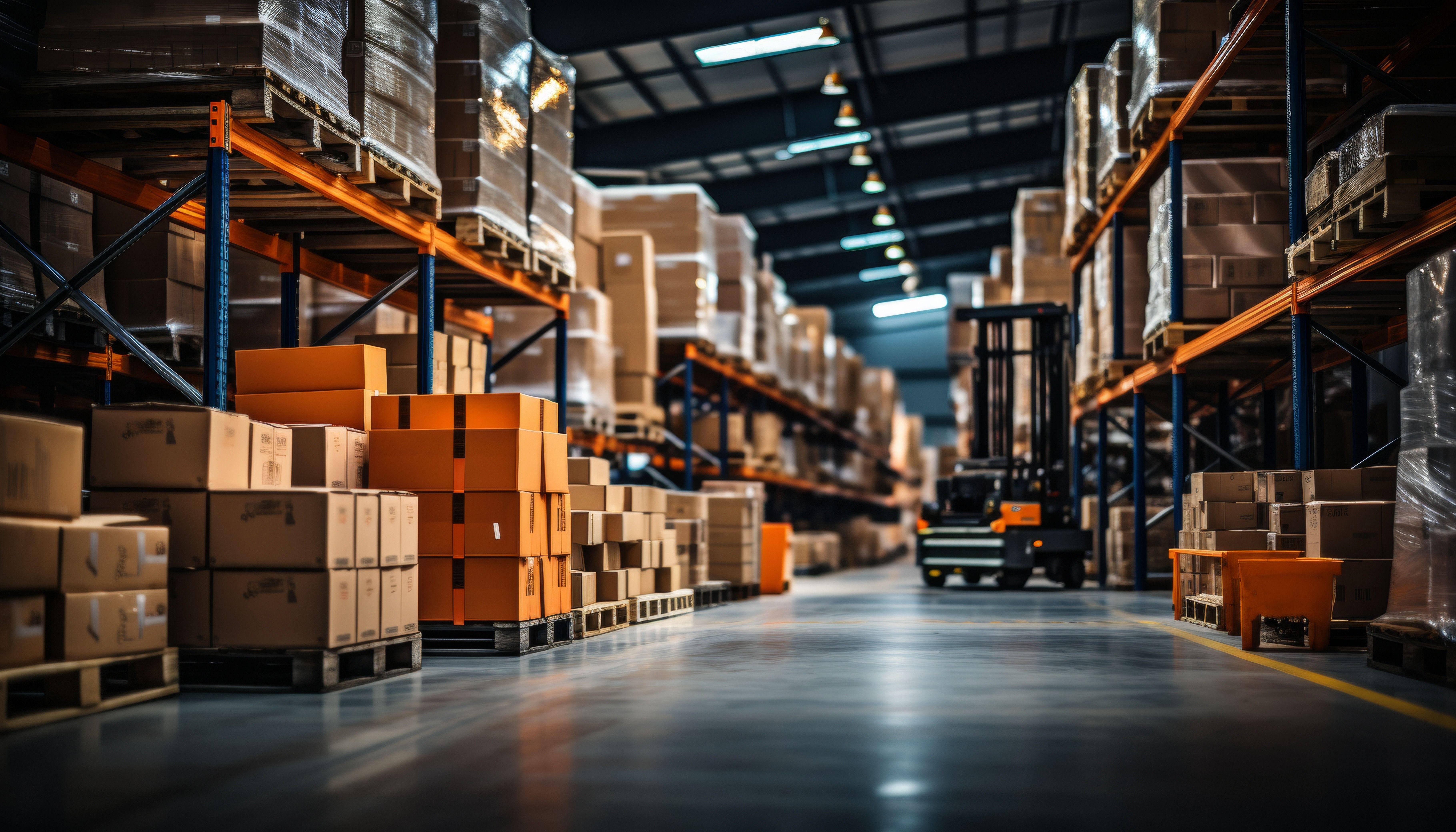
A shuttle system runs on a simple series of automated steps.:
Shuttle Activation: When workers need to retrieve an item, they first type instructions into the control panel or the warehouse management system (WMS). This information usually includes a description of the desired product and its location. The control panel then sends these instructions as commands to the shuttle vehicles, directing them to the product's location.
Loading and Placement: Depending on how the shuttle system is built, this step can be performed in one of two ways. In one case, a conveyor moves the pallet with the product to the shuttle's entry point and places it directly into the shuttle vehicle; in another case, the shuttle vehicle moves along the rails to find the right product on its own.
Movement: Using motors and guided by rails, the shuttle vehicle moves the pallet, either through lift systems or conveyors, to the location for the next stage of the process (e.g., sorting, packing, etc).
The warehouse shuttle system can be set up to run in FIFO (First In, First Out) or LIFO (Last In, First Out), depending on the operation’s needs.
Benefits of Shuttle Systems in Warehousing
Here are some of the benefits of a warehouse shuttle system
- Maximizes Storage Density: Shuttle systems optimize vertical and horizontal space, reducing the need for multiple aisles. This is perfect for operations with large inventories but tight spaces.
- Increased Productivity & Efficiency: Shuttle systems, like Stingray from TGW Logistics, speed up the process of storing and retrieving pallets. This results in less time spent on repetitive tasks, allowing for more focus on problem-solving, maintenance, and other higher-value operations.
- Enhanced Safety: Shuttle systems reduce the risk of accidents and increase workplace safety by reducing forklift use in storage aisles.
- Increases accuracy: Using logistics automation, shuttle systems reduce human errors in handling and locating inventory. This system tracks pallets, lot numbers, and expiration dates to ensure the correct items are picked and shipped.
- Versatility for FIFO and LIFO Operations: Warehouse shuttle systems can handle various load sizes and access multiple levels within racks. They integrate seamlessly with different conveyor systems and can be easily expanded by adding more shuttle robots. This flexibility helps businesses grow their storage and throughput without major warehouse overhauls.
Challenges of Implementing Shuttle Systems
- High Initial Investment: Setting up a shuttle system—hardware, software, and all the infrastructure—can be costly. For some businesses, this can be a considerable upfront investment.
- Maintenance: Warehouse shuttle systems need regular check-ups to keep them running smoothly. A breakdown or malfunction could lead to downtime, affecting order fulfillment and overall efficiency.
- Operational Cost: Additional labor results in higher operational costs and occasionally necessitates extra training for the team to stay ahead of any complex issues.
Final Thoughts
Warehouse shuttle systems are game-changers in modern logistics. They offer increased efficiency, storage density, and safety. By automating the movement of goods, they streamline operations and reduce human error, allowing businesses to keep pace with high demand and tight timelines.
But with all the benefits, the upfront cost and ongoing maintenance can be challenging for some companies to manage. But, with the long-term gains in productivity and accuracy, shuttle systems are a solid investment for businesses to stay competitive through efficient warehouses.
Share this
Contributor
Staff
The team of expert contributors at Businessabc brings together a diverse range of insights and knowledge from various industries, including 4IR technologies like Artificial Intelligence, Digital Twin, Spatial Computing, Smart Cities, and from various aspects of businesses like policy, governance, cybersecurity, and innovation. Committed to delivering high-quality content, our contributors provide in-depth analysis, thought leadership, and the latest trends to keep our readers informed and ahead of the curve. Whether it's business strategy, technology, or market trends, the Businessabc Contributor team is dedicated to offering valuable perspectives that empower professionals and entrepreneurs alike.
previous
Essential Checks When Purchasing a Pre-Owned Shipping Container
next
How to Choose the Best CNC Router for Your Workshop