business resources
Smart Solutions for Improving Manufacturing Output
4 Jan 2025, 4:14 am GMT
In the ever-evolving landscape of manufacturing, maximizing output while maintaining quality is crucial for success. Businesses today face the dual challenge of increasing productivity and ensuring cost-effectiveness. This necessitates proactive strategies, innovative technologies, and a thorough understanding of both processes and workforce capabilities. From automation to improved training programs, manufacturers are exploring numerous avenues to enhance their output. By adopting smart solutions, companies can not only boost their efficiency but also remain competitive in an increasingly complex market. This article delves into effective strategies that manufacturers can implement to achieve these goals.
Embracing Automation and Robotics
Automation and robotics have transformed manufacturing processes by increasing speed and precision while reducing labor costs. These advanced technologies can perform repetitive tasks consistently, thus minimizing human error. Implementing automated systems also allows for 24/7 operations, significantly increasing production capacity. Companies investing in robotic solutions have reported up to a 20% increase in output within months of implementation. For instance, deploying robotic arms for assembly lines streamlines operations, creating a more efficient workflow. Moreover, modern automation technologies are scalable, making it easier for manufacturers to adapt as their production needs evolve. Investing in automation not only enhances production rates but also frees up skilled workers to focus on more complex tasks. The integration of technologies such as laser beam welding, which offers precision and efficiency, can also be found at https://ebindustries.com/laser-beam-welding/ for instance. This combination of automation and advanced welding techniques illustrates the potential of smart manufacturing.
Implementing Lean Manufacturing Principles
Lean manufacturing is centered around maximizing value while minimizing waste. By adopting lean principles, manufacturers can identify and eliminate inefficiencies in their production processes. Techniques such as value stream mapping help visualize the flow of materials and information, allowing for targeted improvements. For example, companies often find that reorganizing their workspace can lead to significant time savings in manufacturing processes. Continuous improvement is a critical aspect; establishing a culture of regular assessment ensures that any operational issues are promptly addressed. Additionally, training employees on lean principles is vital for fostering a proactive workforce that strives for efficiency. Successful implementation of lean strategies can lead to reduced lead times, improved product quality, and increased worker satisfaction. Studies indicate that organizations practicing lean manufacturing can see an output increase of up to 30%. The focus on value stream management promotes sustainability and long-term growth.
Investing in Employee Training and Development
The skillset of a workforce directly impacts a manufacturing entity's overall output. Continuous training and development programs ensure that employees are up to date with the latest technologies and techniques. Organizations that prioritize employee education often witness a notable improvement in productivity and morale. Workers who feel valued and invested in their own growth are typically more engaged and efficient. By implementing cross-training, manufacturers can enhance workforce flexibility, allowing team members to perform multiple roles as needed. This adaptability is especially crucial in times of fluctuating demand. Furthermore, promoting a culture of learning bolsters communication, fostering collaboration among employees. Establishing mentorship programs also aids in knowledge transfer and skills development. Overall, investing in employee growth leads to higher retention rates and improved manufacturing output.
Leveraging IoT and Smart Technologies
The Internet of Things (IoT) is revolutionizing manufacturing by providing real-time data that enhances decision-making. By connecting machinery and equipment, manufacturers can monitor performance and detect issues before they escalate into major problems. Predictive maintenance is a key advantage, allowing companies to schedule repairs during non-peak hours, and minimizing downtime. IoT devices can also optimize inventory management, ensuring that materials are available when needed without overstocking. This efficiency translates directly to improved production flow and lower operational costs. Furthermore, smart technologies can analyze data trends to identify areas for enhancement, empowering manufacturers to adapt swiftly to market changes. With the implementation of IoT, manufacturers can achieve a competitive edge by optimizing operations and boosting output.
Enhancing Supply Chain Collaboration
Effective communication and collaboration across the supply chain significantly impact manufacturing output. Suppliers, manufacturers, and distributors must work together cohesively to streamline processes. By utilizing shared digital platforms, companies can foster transparency, improving lead times and reducing errors. Engaging in regular reviews of supply chain processes also allows for the identification of bottlenecks and areas for improvement. This collective approach not only enhances relationships among partners but also leads to a more agile and responsive manufacturing process.
Utilizing Data Analytics for Continuous Improvement
Data analytics plays a pivotal role in informing manufacturing strategies. Collecting and analyzing data from various stages of the production process can reveal trends that otherwise might remain unnoticed. For example, monitoring machine performance data can highlight inefficiencies and allow for timely interventions. Predictive analytics can also forecast demand, enabling manufacturers to adjust their output accordingly. By implementing data-driven decision-making, manufacturers can continuously enhance their processes, leading to improved productivity. Moreover, adopting key performance indicators (KPIs) enables organizations to measure progress and fine-tune their operations effectively. Analyzing customer feedback through data analytics can also refine product quality and design.
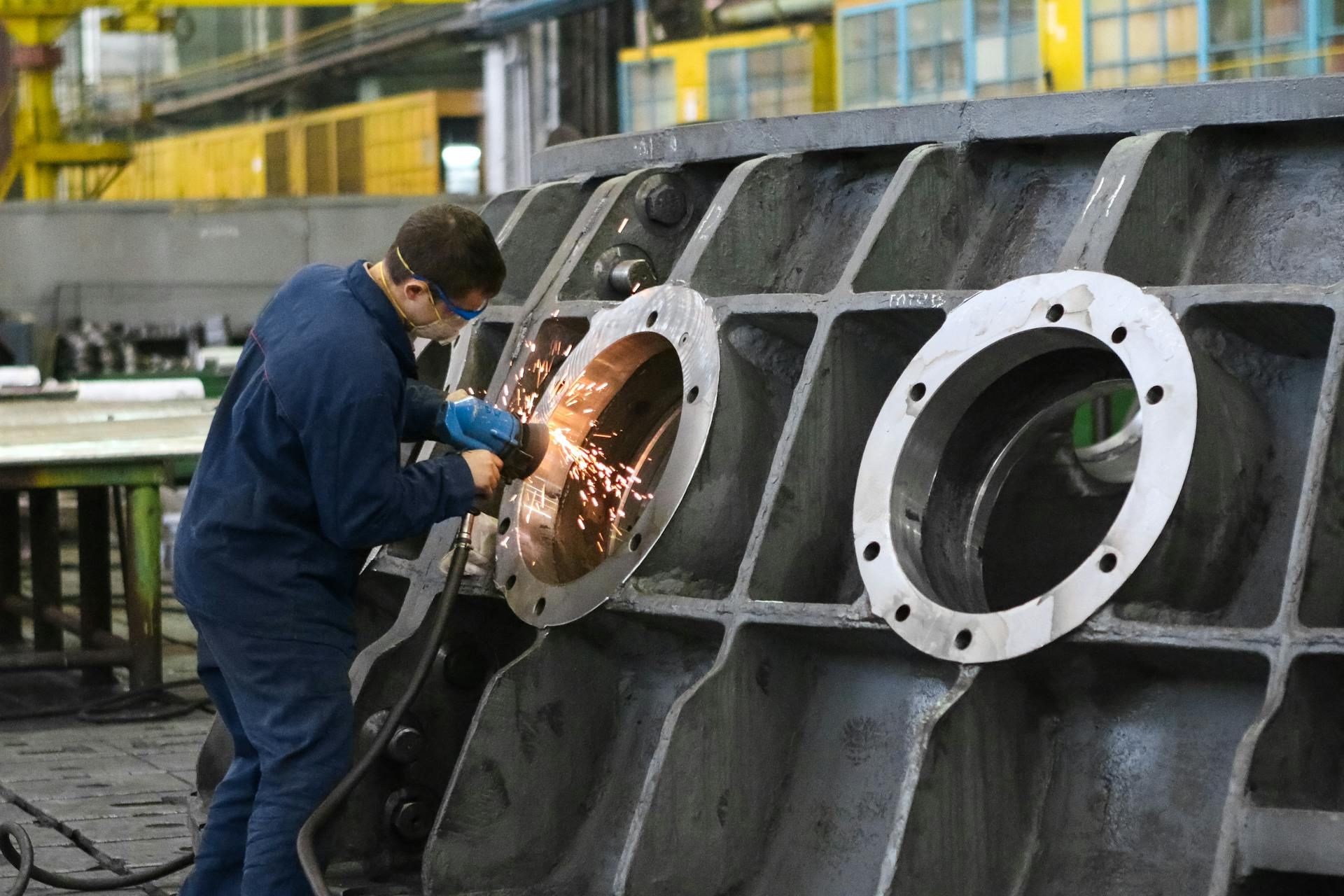
By embracing a range of smart solutions such as automation, lean principles, employee development, IoT, and innovation, manufacturers can significantly enhance their output. The successful implementation of these strategies can lead to increased efficiencies, reduced waste, and improved workforce satisfaction.
Share this
Arthur Brown
Writer
A dad of 3 kids and a keen writer covering a range of topics such as Internet marketing, SEO and more! When not writing, he's found behind a drum kit.
previous
Essential Tips for Maximizing Returns on Real Estate Investments
next
How to Showcase Leadership in Your MBA Application