business resources
Why Quality Industrial Equipment Makes a Difference in Heavy-Duty Performance
9 Apr 2025, 3:24 pm GMT+1
In heavy industry, performance isn’t just about speed or raw strength. It's about reliability, consistency, and longevity under pressure. The machinery in these environments doesn’t get a break—it’s expected to function in punishing conditions day after day. That’s why the quality of the equipment matters just as much as the skill of the operator or the precision of the process. When the tools are subpar, the entire operation feels it. Downtime increases, costs rise, and safety takes a hit. But when the right equipment is in place—well-designed, built to last, and tested in real-world conditions—everything runs smoother, longer, and with fewer unexpected issues.
Engineered for Efficiency
At the heart of any industrial system is the way it's designed to perform over time. Quality equipment is built not just to handle the job but to do it with the least amount of waste—whether that waste is energy, time, or physical effort. Machinery that’s properly engineered runs cooler, makes fewer errors, and doesn’t need to be constantly adjusted or tweaked. This level of performance starts with design and continues through materials, assembly, and testing. So, workstation cranes are often chosen not because they lift more than traditional options, but because they do so with precision and minimal strain on workers. They streamline motion and improve workflow, reducing the physical effort required and keeping operations consistent throughout long shifts. The design behind this kind of equipment prioritizes simplicity in operation and sophistication in construction, meaning fewer breakdowns and more output per hour.
Reducing Downtime, Increasing Reliability
Unplanned stoppages are one of the biggest threats to productivity in heavy-duty environments. When machinery breaks down, it doesn’t just stop working—it often halts an entire process or line, causing ripple effects that reach into inventory, shipping, labor scheduling, and customer satisfaction.
High-quality equipment dramatically lowers the likelihood of these interruptions. It's not just that it fails less often—though that's certainly part of the equation—it also recovers faster. Replacement parts are easier to source, maintenance procedures are clearer and more efficient, and diagnostics are built into the system to catch issues before they escalate. That means problems are caught early, addressed quickly, and resolved with minimal disruption. A single day without unplanned downtime often pays for the added investment in higher-quality tools.
Consistency in Every Operation
Every weld, lift, cut, or press has to meet exacting standards. That kind of consistency can't be left to chance. When equipment isn't reliable, the process suffers—and so does the end product. In industries where precision matters, whether it’s automotive manufacturing or steel fabrication, consistency equals profit.
Low-quality machinery drifts out of calibration, overheats, vibrates excessively, or simply performs unevenly across shifts. Quality tools, in contrast, are built to maintain their precision under load and over time. This helps teams meet production targets without sacrificing quality or safety. It also means that operators can develop repeatable workflows that maximize both speed and accuracy because they can count on the tools to behave the same way every time.
Safety Without Compromise
Heavy-duty work comes with heavy-duty risks. From crushing hazards to electrical failures, the stakes are high when something goes wrong. Cheap or outdated machinery increases those risks. It’s not just about mechanical failure—it’s about poor design, lack of redundancy, and the inability to cope with real-world stress.
High-quality industrial equipment is built with safety as a core element, not a secondary feature. Guarding is better thought out, controls are intuitive, and emergency features are standard. Equipment that’s been designed and tested for demanding conditions tends to hold up under pressure—not just physically but in terms of how it supports the people who work around it. Workers can focus on doing their jobs rather than compensating for machines that aren't up to standard.
This attention to safety translates to fewer injuries, lower insurance costs, and better morale. And when teams trust their tools, they work faster and with greater confidence, which brings its own performance advantages.
Lower Total Cost Over Time
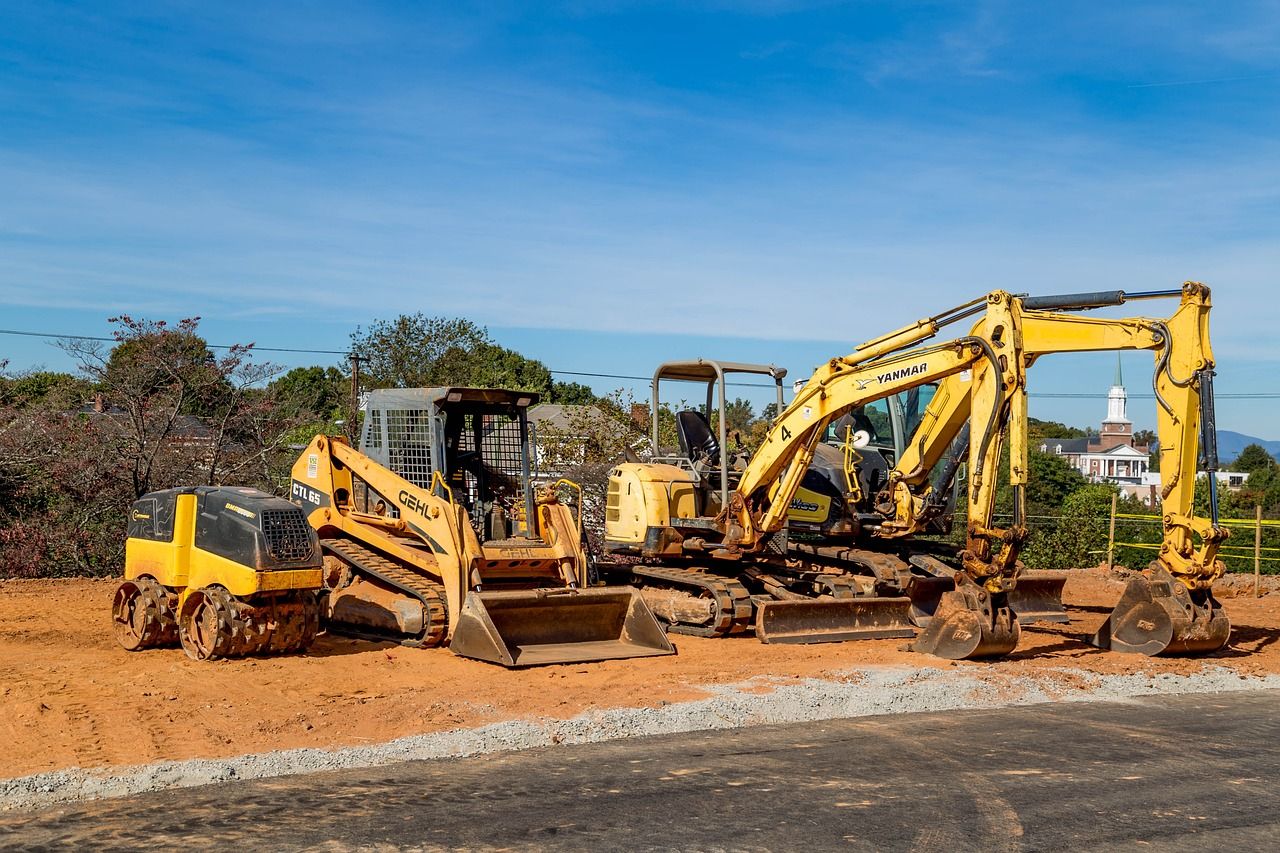
One of the main arguments against investing in higher-end industrial equipment is the upfront price. However, when the costs are tracked over the lifetime of the equipment, the picture changes. Machines that cost less to purchase often cost far more to operate. They break more often, use more energy, and wear out faster. They might seem like a bargain until the maintenance bills, repair calls, and replacement parts start piling up.
By contrast, higher-quality equipment tends to run longer before needing service, and when it does, the service is easier and more predictable. The machines hold their value better, too, which can be a factor when it's time to upgrade or sell. Over ten years, a well-built piece of machinery often ends up being far less expensive than a cheaper version that needs to be replaced after three or four.
Quality industrial equipment isn't a luxury or an optional upgrade—it’s the foundation of reliable, high-performing operations. It delivers measurable gains in efficiency, reliability, safety, and long-term cost while helping skilled workers perform at their best.
Share this
Arthur Brown
Writer
A dad of 3 kids and a keen writer covering a range of topics such as Internet marketing, SEO and more! When not writing, he's found behind a drum kit.
previous
Best Practices for Ensuring Quality Standards in Indie Game Production
next
Studio Ghibli AI trend: Expert warns it could come at a cost - hidden dangers you need to know