business resources
The Backbone of Manufacturing: How Injection Molding Powers Key Industries
30 Jan 2025, 3:58 pm GMT
Injection molding is the backbone of modern manufacturing, shaping the way industries produce high-quality, cost-effective, and durable components. From automotive to healthcare, this versatile process ensures precision, scalability, and efficiency, making it indispensable in today’s fast-paced industrial landscape.
By injecting molten material into custom molds, manufacturers can create complex designs with minimal waste and rapid production times. This technology drives innovation across multiple sectors, enabling the production of everything from medical devices to consumer electronics.
In this article, we’ll explore six key ways injection molding powers major industries, highlighting its advantages and why it remains a cornerstone of industrial production. Let’s dive in.
Enhances Performance and Efficiency in the Automotive Industry
Injection molding is a driving force in the automotive industry, enabling the production of lightweight, durable components that improve vehicle performance and fuel efficiency. From dashboards and bumpers to intricate engine parts, manufacturers rely on this process to create high-precision, cost-effective components. For instance, with AIM Processing injection molding, automakers can produce complex plastic parts that meet strict safety and durability standards while reducing overall vehicle weight. This translates to better fuel economy, lower emissions, and enhanced design flexibility.
As electric and autonomous vehicles gain popularity, injection molding continues to support innovation, allowing for the development of advanced, high-performance materials that shape the future of automotive manufacturing.
Ensures Precision and Sterility in the Medical Industry
The medical industry depends on injection molding for the mass production of sterile, high-quality components used in life-saving equipment. From surgical tools and IV connectors to prosthetic parts and diagnostic devices, injection molding ensures accuracy and consistency in medical manufacturing. The process allows for the creation of intricate designs with tight tolerances, ensuring that each component meets stringent healthcare regulations.
Medical-grade plastics also offer biocompatibility and resistance to chemicals, making them ideal for single-use applications that minimize contamination risks. Manufacturers can produce customized medical components with precise detailing and high-volume efficiency, ensuring that hospitals and clinics have reliable, safe medical devices. As demand for advanced medical technology grows, injection molding continues to support the industry with innovative solutions.
Enables Compact and Durable Designs in the Electronics Industry
Injection molding is essential in the electronics industry, where precision, miniaturization, and durability are key factors. It enables the production of intricate plastic housings, circuit board components, and insulation materials that protect delicate electronic systems. With increasing demand for smaller, more powerful devices, manufacturers rely on injection molding to produce lightweight yet sturdy casings that offer excellent heat resistance and electrical insulation.
The process also allows for overmolding, where different materials are combined to enhance functionality, such as rubberized grips on handheld devices. Injection molding ensures cost-effective mass production without compromising quality, making it indispensable for consumer electronics, smart devices, and industrial control systems. As technology advances, injection molding will continue to push the boundaries of design and innovation in electronics.
Supports Lightweight and High-Performance Parts in Aerospace Industry
The aerospace industry benefits significantly from injection molding due to its ability to produce lightweight, high-strength components with exceptional precision. Aircraft and spacecraft require materials that can withstand extreme temperatures, pressure, and mechanical stress while remaining as light as possible to improve fuel efficiency. Injection-molded thermoplastics and composites replace traditional metal parts, reducing overall weight without sacrificing durability. These materials also offer resistance to corrosion and wear, ensuring the longevity of aerospace components.
Injection molding also allows for the rapid production of complex, custom parts, reducing lead times and costs for manufacturers. As space exploration and commercial aviation continue to expand, injection molding will remain a key manufacturing process, supporting the development of cutting-edge aerospace technologies.
Delivers Customization and Mass Production in the Consumer Goods Industry
From household appliances to sporting goods, injection molding is a cornerstone of the consumer goods industry. It allows manufacturers to produce large volumes of identical products while maintaining high quality and cost efficiency. This process enables the creation of everything from kitchen utensils and storage containers to toys and fitness equipment. The ability to use a wide range of plastics, including eco-friendly and biodegradable materials, also supports sustainable product development.
Injection molding provides versatility in design, allowing for customized textures, colors, and branding elements that enhance product appeal. Whether it’s ergonomic grips on tools or sleek, durable smartphone cases, injection molding continues to shape the everyday products that consumers rely on.
Enhances Sustainability and Product Protection in the Packaging Industry
The packaging industry relies on injection molding to produce strong, lightweight, and visually appealing packaging solutions. Food containers, bottle caps, and protective casings for fragile items all benefit from the precision and efficiency of this process. Injection-molded packaging not only ensures product protection during storage and transportation but also enhances shelf appeal with sleek, customizable designs.
Advances in biodegradable and recycled plastics have made injection molding a more sustainable option, helping companies reduce their environmental footprint. With the rise of e-commerce and demand for sustainable packaging, injection molding continues to drive innovation by offering eco-friendly alternatives without compromising durability or functionality.
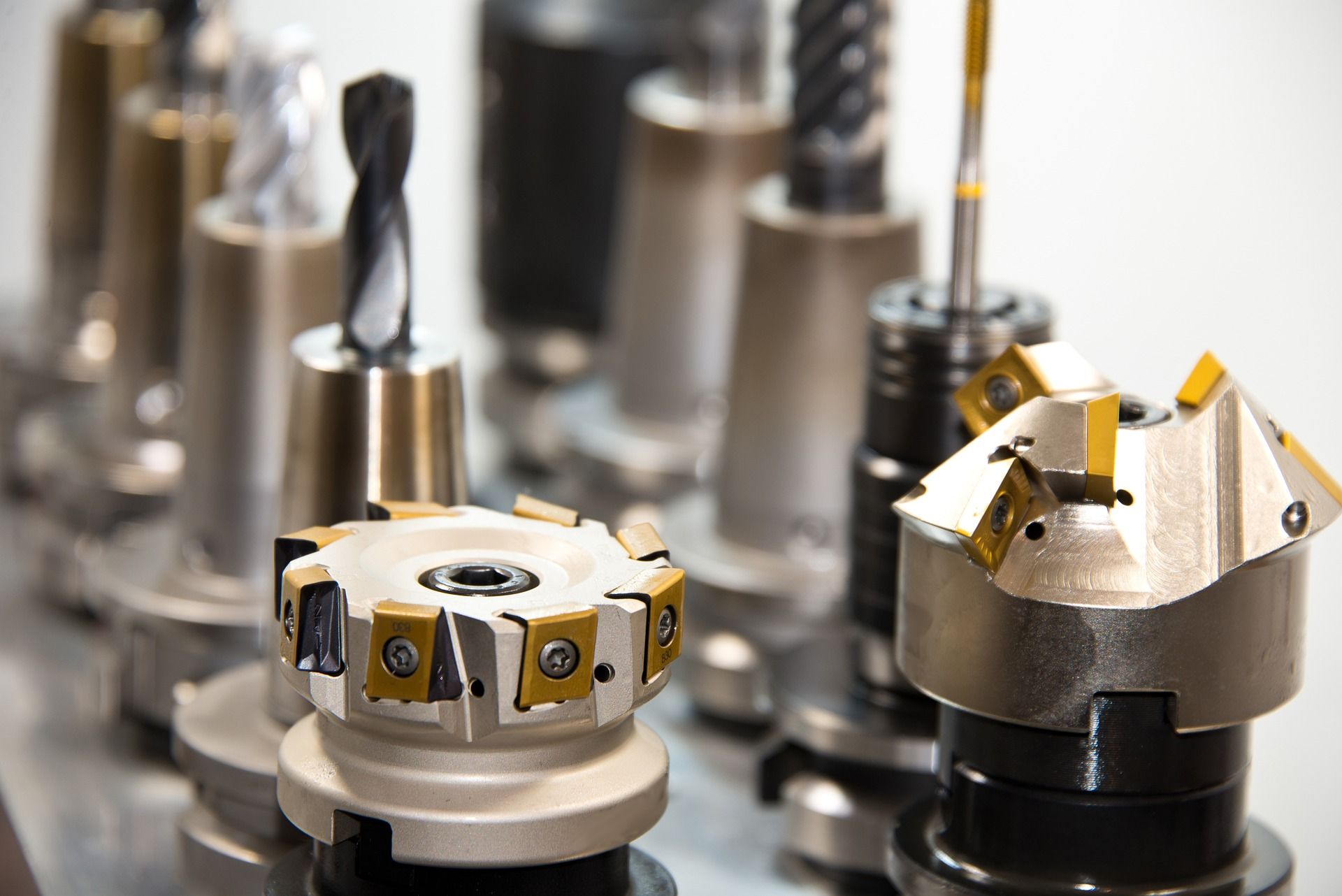
Injection molding is a powerhouse in modern manufacturing, driving efficiency, innovation, and cost-effectiveness across multiple industries. From automotive and aerospace to medical devices and consumer goods, this process ensures precision, durability, and scalability in production. Its ability to create complex, lightweight, and high-strength components makes it indispensable for businesses seeking high-quality, mass-produced parts. As technology advances, injection molding continues to evolve, incorporating sustainable materials and cutting-edge techniques to meet industry demands.
Share this
Arthur Brown
Writer
A dad of 3 kids and a keen writer covering a range of topics such as Internet marketing, SEO and more! When not writing, he's found behind a drum kit.
previous
Why promotional codes are a two way street
next
6 Practical Tips for Smoother Business Operations